pifpaf
New member
It has been ten years since the late Nicolas Hayek warned that he was going to cut the deliveries of ebauches to his competitors.
While some brands, like Breitling or Panerai, did their best to integrate their production as much as possible, some others, like IWC for example, did not seek to develop other house-made movements, to compensate for a possible ending of the precious 7750 and 2824 deliveries.
Whether they are ants or cicadas, hard workers or lazy, nobody foresaw the current core issue, which actually has to do with the "heart" of the watch.
Indeed, the end of the Swatch group deliveries had been well anticipated by the "shavings makers" (like Tech Ebauches, Sellita, Technotime, Concepto, etc.…), who created a "CNC" Maginot line.
But the fate of Maginot lines is to be by-passed: actually, the problem specifically comes from the hairsprings and more generally from the sets! In fact, the main provider, Nivarox, is a subsidiary of the Swatch Group...
More opinions (by famous bloggers), a Pool to give your opinion, on the watchonista's silicium page.
For a few months, there was a rumor about a potential wave of panic related to the hairsprings: it stated that this component, as tiny as it is vital, as cheap as it is complicated to industrialize, would be missing with a cruelty worthy of the quartz crisis.
This anxiety became tangible when Nivarox informed TAG Heuer that the deliveries had stopped.
Today, a watchmaker who wants to produce watches independently, has to invest in equipments. Yet, there are only three ways to do so.
Produce Elinvar hairsprings oneself: if it is the most common and the safest solution in terms of brand image, it is also the most complicated to implement.
Indeed, the material's recipe is not a secret, the Elinvar alloys are utilized in precision measurement tools (industrial scales, precision gauges, etc.);
Hence, there are some producers of the precious isotropic steel alloy, most of them German;
For example, one could think of the Precision Engineering/Moser share holder, who has been producing this material for a long time.
The product is available, the Elinvar spiral recipe is can be found in all the good watchmaking cooking books.
But the missing part is the Chef! Only a few members of Nivarox, carefully selected and submitted to security and confidentiality levels that would make a fighter pilot turn pale, know the secrets of fabrication of the magical hairsprings produced by the ETA's subsidiary.
The brands who offers alternative hairsprings, like Ato-Kalpa or Technotime, spent years to produce good quality hairsprings, and the waste seems to be higher than that of the Swatch Group ("seems", because nobody knows what happens at Nivarox).
So, to summarize:
Finding the right alloy is rather easy, and at any rate a hairspring only weighs a few tenths of a gram, therefore one wastes very little material to find the right mix.
Finding the machines for laminating, wire drawing and hairspring counting is far more complicated, as they are not produced anymore and most of them were destroyed during the quartz crisis.
For example, Technotime bought machines from the ex-Eastern Bloc, formerly used to produce Poljot and consorts.
Finding the "Chef" who will perfectly master all the stages of the production is almost impossible; therefore, he must be trained internally.
The implementation of a hairspring production plant is a long process, as it takes several years of development to achieve a consistent level of quality (consistent enough for the pairing and the hairspring/balance tuning to be done in less than one day per watch).
But! As the recent "TAG case" just demonstrated, most of the brands cannot spend the 5 or 10 years required to integrate the whole production chain.
Buy hairsprings from other providers than Nivarox: in spite of the quality of their production, the likeable Helvetian sub-contractors cannot supply quantities large enough for the big brands such as Tag Heuer (or Breitling).
TAG, as always the first in any domain, just announced that it will buy its supplies from Japan.
The only continent that produces hairsprings in large quantities is Asia.
For example, one could think of the Chinese Sea-Gull, whose production figures are bigger than those of ETA.
Or of SeikoSha, which is also a very good alternative choice, as its Grand Seiko watches announce better chronometric performances than Rolex.
The Helvetian brands which will source their products in Asia, will symbolically trample the "Swiss Made", by fitting the Swiss watches with the only part that until now, was 100% made in Switzerland.
This decision might lead to extremely damaging consequences.
One already sees some small brands claiming their cantonal belonging, since the "Swiss Made" doesn't seem to be a guaranty of AOC for the watches.
Indeed it will be the end of a kind of ambiguity; but the overall watchmaking industry benefits from it;
and the entire field, even those who did what it takes, is at risk of being penalized by a blurred brand image.
Produce silicon hairsprings: it is currently the biggest topic in watchmaking since the advent of quartz.
To well understand what is at stake, one has to understand that the preparation of silicon compared to that of Elinvar is like the Molecular Gastronomy opposed to the "Nouvelle Cuisine" of the greatest chefs.
Or even, if one is a scandalmonger, it is like McDonald's vs. the "Grande Cuisine".
While manufacturing Elinvar demands a genius cook able to feel the materials, to observe the clouds to know the atmospheric pressure, the fabrication of silicon hairsprings takes a valedictorian trained in cutting-edge technologies and able to run the chemical cutting of material with precisions down to the micron, through the mathematical rigor of equations.
The benefit of using silicon is that one can implement a manufacturing chain faster.
If there is enough equipment, this strategic component can be produced in large quantities far quicker than the Elinvar.
The other benefit brought by the silicon is that the quality of the hairsprings is standardized by the "LIGA" cutting process.
Hence, the slow and difficult pairing phase does not exist anymore (the differences in hairsprings qualities are compensated by appropriate balances). Thus, even the balance production stage is simplified.
The problem with the silicone arises during the assembling phase, where the very fragile hairspring must be fitted into its final slot without shocks.
To better understand the two "quick" options, Silicon & Asia, let's take a careful look at the Tag Heuer case:
The rumor states that LVMH's legal department more or less challenged their counterpart at Swatch Group.
LVMH wanted to speed up the process of contract renewal for the deliveries of Nivarox escapement sets.
But the Swatch Group lawyers outsmarted those of LVMH: they cut the sets deliveries to Tag Heuer, without striking a blow. Considering the suddenness of the announcement, TAG did not have time to develop its own Invar sets. Therefore, there were only two options: Asia or Silicon.
To compensate for the withdrawal of Nivarox, TAG once again called upon Seiko (and this after the caliber 1887) to get out of this tricky situation.
To address the problem, TAG could have developed homemade silicon;
but they chose to rely on Seiko, on the one hand because it was obviously simple from a logistical standpoint, and on the other hand because the image of silicon may have been deemed dangerous.
Actually, the crucial question raised by TAG's choice is this: what does a "region of origin" mean?
Is it the use of traditional technologies, implying the utilization of a plain alloy and lots of handwork, but made in Asia?
Or does it mean a totally normalized production with cutting-edge industrial processes, but made in Juras?
And the other reason to reject silicon certainly was the reliability.
The fundamental obsessions at Rolex are the reliability and the after sale returns.
As a matter of fact, it is one of the reasons why their production processes are widely automated.
Rolex is undoubtedly the most automated of the mid-range market brands in the Swiss watchmaking industry.
It is obvious that Rolex made the reduction of costs a priority. But not only that!
Rolex engineers spend their time burying innovations.
These break-through, which would have benefited certain independent brands for years, are buried by Rolex without second thought.
This policy of generalized industrialization and of slow innovation, of course, comes from the necessity to bring down the after sales servicing figures.
The brand with a crown would never launch an innovation without making sure to master the consequences from A to Z. One even knows that the brand is very advanced on the silicon matter, but sticks however to the excellent Parachrom rather than taking chances with the silicon.
In addition, it is a common knowledge that Omega, like De Bethune or other "early adopters", already underwent the difficult development of this cutting-edge technology. For that matter, they deserve praises.
For the great watchmakers (such as Journe or Flageollet), Abraham Louis Breguet's Holy Grail was to use less lubrication, which is a source of problems and of dirt accumulation in the mechanism.
For example, with the Extreme Lab, Jeager LeCoultre tested the "fat-free" watch (with a limited success).
If the silicon technology breaks through, there is no doubt that the JlC EL will go through the roof of the auctions at Christie's, 50 years from now, since it has been emblematic of the beginnings of this "fat free" technology.
But today, with the waterproof watches and high quality lubricants, does the development of a lubricant-free technology still make sense?
The greatest technical achievements , like the Citroen DS, the iPhone 4 , the Concorde or printing, were very difficult to develop, which frustrated many clients (-guinea pigs).
But these long development phases have been laboratories for innovations, which were reused in hundreds of new similar products (for example, the technologies developed for the Concorde are still utilized in nowadays airliners).
The equivalent in watchmaking is the Omega 8500, with its silicon hairspring, its coaxial escapement and its double barrel;
it is currently the pinnacle of the mainstream watchmaking technology, but it inevitably suffers from an after sales servicing rate higher than the Rolex 3135.
So, are we ready to potentially sacrifice the long term reliability, in order to benefit from a state-of-the-art product?
Furthermore, when one talks about watchmaking, the cutting edge technology does not mean the same thing.
In the automotive or the mobile phone fields, the equation is relatively straightforward; the goal is mainly to reach the most advanced technology.
"Mainly" , because if some car makers , leaders from a technological standpoint, are successful, their German counterparts, not always as technically advanced, are even more successful !
In the end, the Teutonic cars take the advantage thanks to their uninterrupted reputation for reliability, prestige and to a certain tradition linked to the German luxury car industry.
From the communists to the capitalists, from the industrials to the organized crime, all, all, all of them did put their renowned bottoms on the Mercedes-Benz stiff leather.
A French rap band (NTM) even sang its ode to the "Benz-Benz-Benz".
Why ? Because Mercedes-Benz is a symbol of tradition. And tradition is a common value to all the cultures.
The reason why I am talking to you about tradition, is because it is the key to the rebirth of the mechanical watchmaking.
In a world where everything moves faster and faster, where one lives in an opulent society steered like a drunken ship, it is reassuring to remember our grand-parents' sacrifices, which allowed for this opulence to exist.
Yet, the mechanical watchmaking's Kryptonite was the quartz.
And there are odd resemblances between the quartz and the silicon: silicon is the main component of the micro-processors that power all our computerized systems, especially the Casio G-Shock.
But also (and specifically?) the fabrication process of a quartz watch is totally standardized, exactly like the production of the sets of silicon escapement devices (compared to the artisanal manufacturing process of a mechanical watch).
Ironically, a well tuned silicon system is amazingly efficient;
the proof is that Technotime, Chopard and Tissot, all of them using silicon hairsprings, won the last International Chronometry Contest.
Yet, the other technology that provides an incredible precision with a silica core is of course the quartz!
The best illustration of this phenomenon is Patek Philippe: the aura of the most prestigious of all brands relies on an uninterrupted tradition of mechanical movements and on the quest for the best quality, by employing the best craftsmen in all Romandie.
So, do we really want a cutting-edge mechanism in a traditional watch?
Watchmaking only makes sense if one agrees to stop the technological progress at a given date.
If he had had the adapted tools during the French revolution era, would Abraham-Louis Breguet have integrated silicon into his watches?
In short, the silicon raises the metaphysical question of when does the hard-line mechanical watchmaking stops evolving; does silicon have its place in a traditional watch?
Conclusion:
The butterfly effect is when a minor decision leads to major consequences.
The ironical side of the story is that, after a few generations, the savior of the traditional mechanical watchmaking could become its gravedigger.
The decision to stop the deliveries of Nivarox sets could be an incentive to switch to silicon.
But the latter is double-edged! It could be the greatest revolution in watchmaking since Huygens (well, at least since the Invar), but it also could be the high-tech product that will totally depreciate the Swiss watchmaking tradition...
We are lucky to witness the greatest revolution in watchmaking since the end of the 60's, and the advent of quartz;
like all the revolutions, it could be a top, or a flop. Will silicon join the heaven of the ground-breaking technologies which died too soon? Or will it open the road to new chronometric heights?
Will it crash against the breakers of the reliability's craggy coasts? Will it rescue the Swiss Made from the Dragons' jaws or definitively spoil the already eared Helvetian watchmaking's brand image?
While some brands, like Breitling or Panerai, did their best to integrate their production as much as possible, some others, like IWC for example, did not seek to develop other house-made movements, to compensate for a possible ending of the precious 7750 and 2824 deliveries.
Whether they are ants or cicadas, hard workers or lazy, nobody foresaw the current core issue, which actually has to do with the "heart" of the watch.
Indeed, the end of the Swatch group deliveries had been well anticipated by the "shavings makers" (like Tech Ebauches, Sellita, Technotime, Concepto, etc.…), who created a "CNC" Maginot line.
But the fate of Maginot lines is to be by-passed: actually, the problem specifically comes from the hairsprings and more generally from the sets! In fact, the main provider, Nivarox, is a subsidiary of the Swatch Group...
More opinions (by famous bloggers), a Pool to give your opinion, on the watchonista's silicium page.
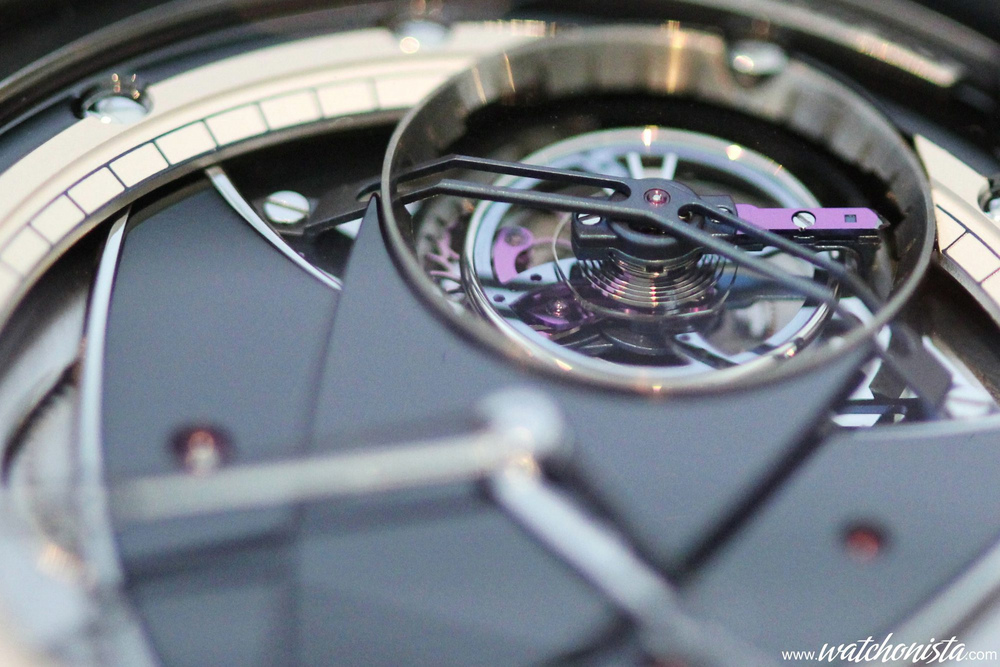
For a few months, there was a rumor about a potential wave of panic related to the hairsprings: it stated that this component, as tiny as it is vital, as cheap as it is complicated to industrialize, would be missing with a cruelty worthy of the quartz crisis.
This anxiety became tangible when Nivarox informed TAG Heuer that the deliveries had stopped.
Today, a watchmaker who wants to produce watches independently, has to invest in equipments. Yet, there are only three ways to do so.
Produce Elinvar hairsprings oneself: if it is the most common and the safest solution in terms of brand image, it is also the most complicated to implement.
Indeed, the material's recipe is not a secret, the Elinvar alloys are utilized in precision measurement tools (industrial scales, precision gauges, etc.);
Hence, there are some producers of the precious isotropic steel alloy, most of them German;
For example, one could think of the Precision Engineering/Moser share holder, who has been producing this material for a long time.
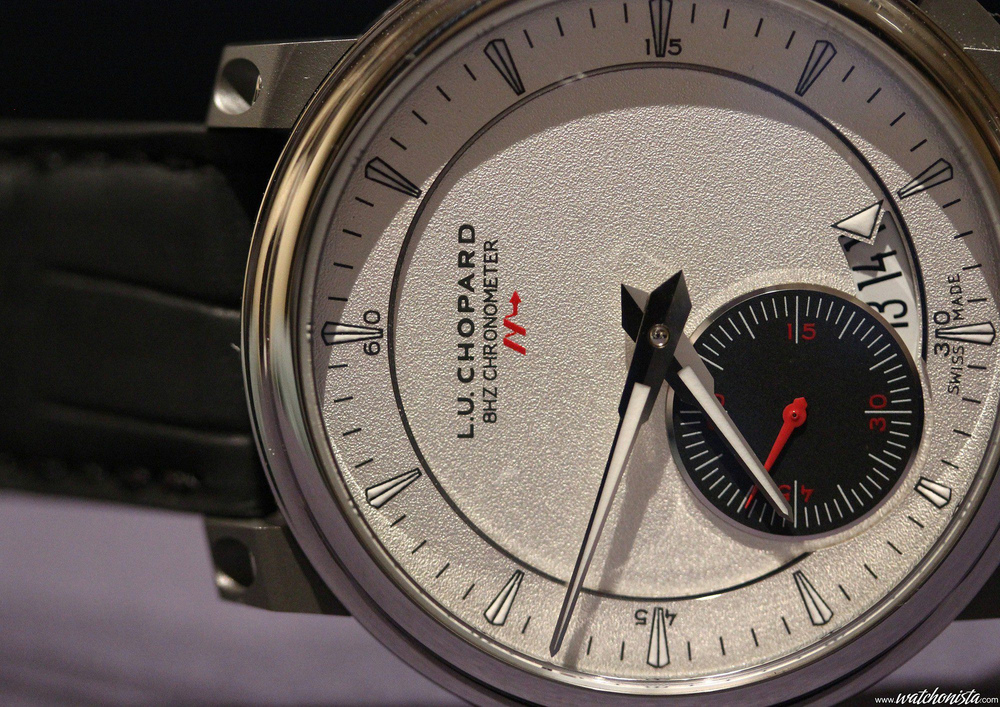
The product is available, the Elinvar spiral recipe is can be found in all the good watchmaking cooking books.
But the missing part is the Chef! Only a few members of Nivarox, carefully selected and submitted to security and confidentiality levels that would make a fighter pilot turn pale, know the secrets of fabrication of the magical hairsprings produced by the ETA's subsidiary.
The brands who offers alternative hairsprings, like Ato-Kalpa or Technotime, spent years to produce good quality hairsprings, and the waste seems to be higher than that of the Swatch Group ("seems", because nobody knows what happens at Nivarox).
So, to summarize:
Finding the right alloy is rather easy, and at any rate a hairspring only weighs a few tenths of a gram, therefore one wastes very little material to find the right mix.
Finding the machines for laminating, wire drawing and hairspring counting is far more complicated, as they are not produced anymore and most of them were destroyed during the quartz crisis.
For example, Technotime bought machines from the ex-Eastern Bloc, formerly used to produce Poljot and consorts.
Finding the "Chef" who will perfectly master all the stages of the production is almost impossible; therefore, he must be trained internally.
The implementation of a hairspring production plant is a long process, as it takes several years of development to achieve a consistent level of quality (consistent enough for the pairing and the hairspring/balance tuning to be done in less than one day per watch).
But! As the recent "TAG case" just demonstrated, most of the brands cannot spend the 5 or 10 years required to integrate the whole production chain.
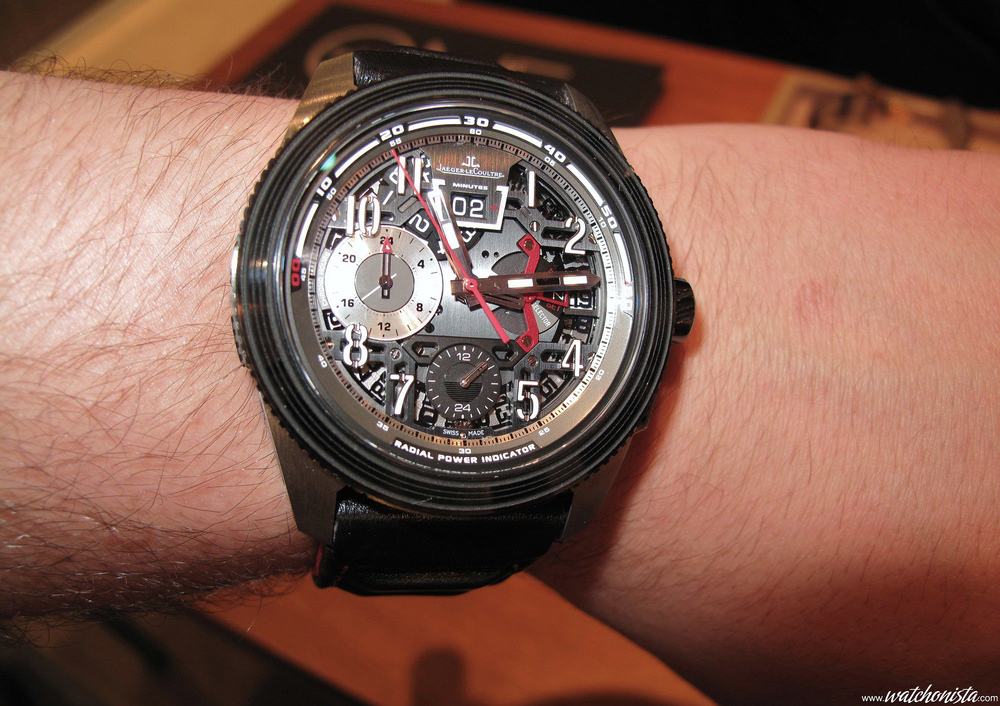
Buy hairsprings from other providers than Nivarox: in spite of the quality of their production, the likeable Helvetian sub-contractors cannot supply quantities large enough for the big brands such as Tag Heuer (or Breitling).
TAG, as always the first in any domain, just announced that it will buy its supplies from Japan.
The only continent that produces hairsprings in large quantities is Asia.
For example, one could think of the Chinese Sea-Gull, whose production figures are bigger than those of ETA.
Or of SeikoSha, which is also a very good alternative choice, as its Grand Seiko watches announce better chronometric performances than Rolex.
The Helvetian brands which will source their products in Asia, will symbolically trample the "Swiss Made", by fitting the Swiss watches with the only part that until now, was 100% made in Switzerland.
This decision might lead to extremely damaging consequences.
One already sees some small brands claiming their cantonal belonging, since the "Swiss Made" doesn't seem to be a guaranty of AOC for the watches.
Indeed it will be the end of a kind of ambiguity; but the overall watchmaking industry benefits from it;
and the entire field, even those who did what it takes, is at risk of being penalized by a blurred brand image.
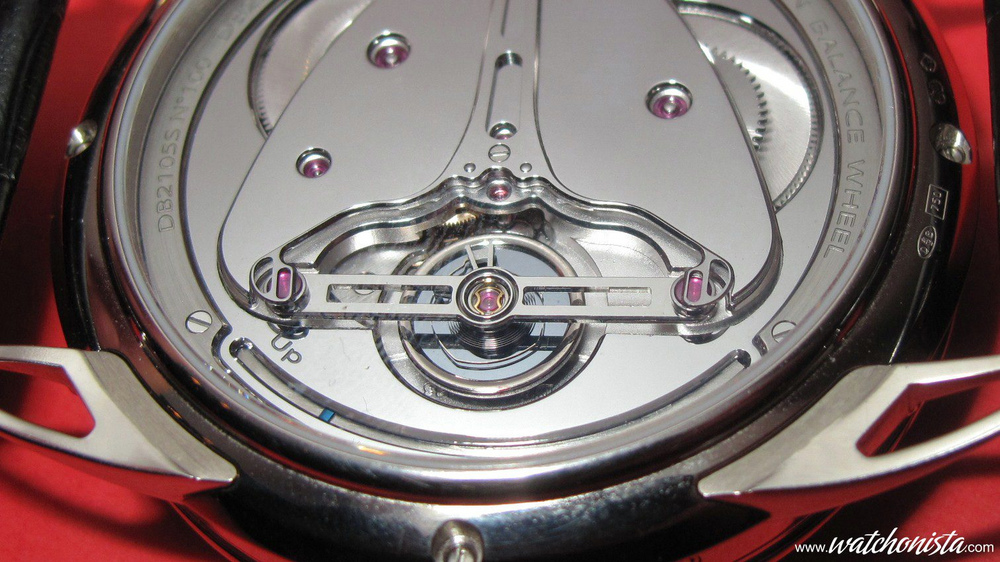
Produce silicon hairsprings: it is currently the biggest topic in watchmaking since the advent of quartz.
To well understand what is at stake, one has to understand that the preparation of silicon compared to that of Elinvar is like the Molecular Gastronomy opposed to the "Nouvelle Cuisine" of the greatest chefs.
Or even, if one is a scandalmonger, it is like McDonald's vs. the "Grande Cuisine".
While manufacturing Elinvar demands a genius cook able to feel the materials, to observe the clouds to know the atmospheric pressure, the fabrication of silicon hairsprings takes a valedictorian trained in cutting-edge technologies and able to run the chemical cutting of material with precisions down to the micron, through the mathematical rigor of equations.
The benefit of using silicon is that one can implement a manufacturing chain faster.
If there is enough equipment, this strategic component can be produced in large quantities far quicker than the Elinvar.
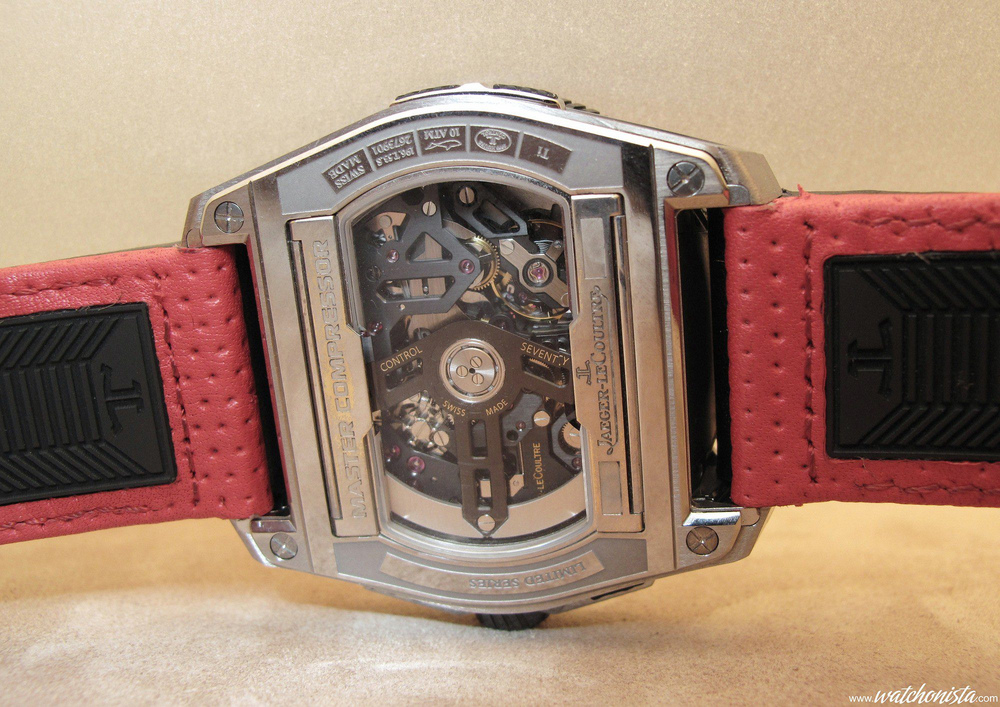
The other benefit brought by the silicon is that the quality of the hairsprings is standardized by the "LIGA" cutting process.
Hence, the slow and difficult pairing phase does not exist anymore (the differences in hairsprings qualities are compensated by appropriate balances). Thus, even the balance production stage is simplified.
The problem with the silicone arises during the assembling phase, where the very fragile hairspring must be fitted into its final slot without shocks.
To better understand the two "quick" options, Silicon & Asia, let's take a careful look at the Tag Heuer case:
The rumor states that LVMH's legal department more or less challenged their counterpart at Swatch Group.
LVMH wanted to speed up the process of contract renewal for the deliveries of Nivarox escapement sets.
But the Swatch Group lawyers outsmarted those of LVMH: they cut the sets deliveries to Tag Heuer, without striking a blow. Considering the suddenness of the announcement, TAG did not have time to develop its own Invar sets. Therefore, there were only two options: Asia or Silicon.
To compensate for the withdrawal of Nivarox, TAG once again called upon Seiko (and this after the caliber 1887) to get out of this tricky situation.
To address the problem, TAG could have developed homemade silicon;
but they chose to rely on Seiko, on the one hand because it was obviously simple from a logistical standpoint, and on the other hand because the image of silicon may have been deemed dangerous.
Actually, the crucial question raised by TAG's choice is this: what does a "region of origin" mean?
Is it the use of traditional technologies, implying the utilization of a plain alloy and lots of handwork, but made in Asia?
Or does it mean a totally normalized production with cutting-edge industrial processes, but made in Juras?
And the other reason to reject silicon certainly was the reliability.
The fundamental obsessions at Rolex are the reliability and the after sale returns.
As a matter of fact, it is one of the reasons why their production processes are widely automated.
Rolex is undoubtedly the most automated of the mid-range market brands in the Swiss watchmaking industry.
It is obvious that Rolex made the reduction of costs a priority. But not only that!
Rolex engineers spend their time burying innovations.
These break-through, which would have benefited certain independent brands for years, are buried by Rolex without second thought.
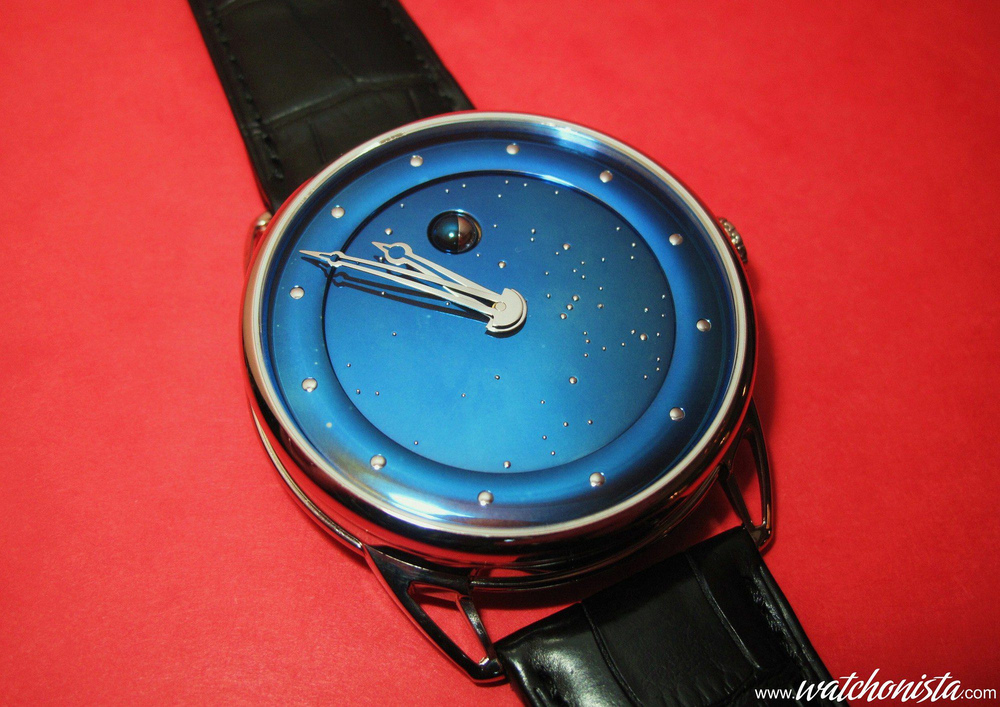
This policy of generalized industrialization and of slow innovation, of course, comes from the necessity to bring down the after sales servicing figures.
The brand with a crown would never launch an innovation without making sure to master the consequences from A to Z. One even knows that the brand is very advanced on the silicon matter, but sticks however to the excellent Parachrom rather than taking chances with the silicon.
In addition, it is a common knowledge that Omega, like De Bethune or other "early adopters", already underwent the difficult development of this cutting-edge technology. For that matter, they deserve praises.
For the great watchmakers (such as Journe or Flageollet), Abraham Louis Breguet's Holy Grail was to use less lubrication, which is a source of problems and of dirt accumulation in the mechanism.
For example, with the Extreme Lab, Jeager LeCoultre tested the "fat-free" watch (with a limited success).
If the silicon technology breaks through, there is no doubt that the JlC EL will go through the roof of the auctions at Christie's, 50 years from now, since it has been emblematic of the beginnings of this "fat free" technology.
But today, with the waterproof watches and high quality lubricants, does the development of a lubricant-free technology still make sense?
The greatest technical achievements , like the Citroen DS, the iPhone 4 , the Concorde or printing, were very difficult to develop, which frustrated many clients (-guinea pigs).
But these long development phases have been laboratories for innovations, which were reused in hundreds of new similar products (for example, the technologies developed for the Concorde are still utilized in nowadays airliners).
The equivalent in watchmaking is the Omega 8500, with its silicon hairspring, its coaxial escapement and its double barrel;
it is currently the pinnacle of the mainstream watchmaking technology, but it inevitably suffers from an after sales servicing rate higher than the Rolex 3135.
So, are we ready to potentially sacrifice the long term reliability, in order to benefit from a state-of-the-art product?
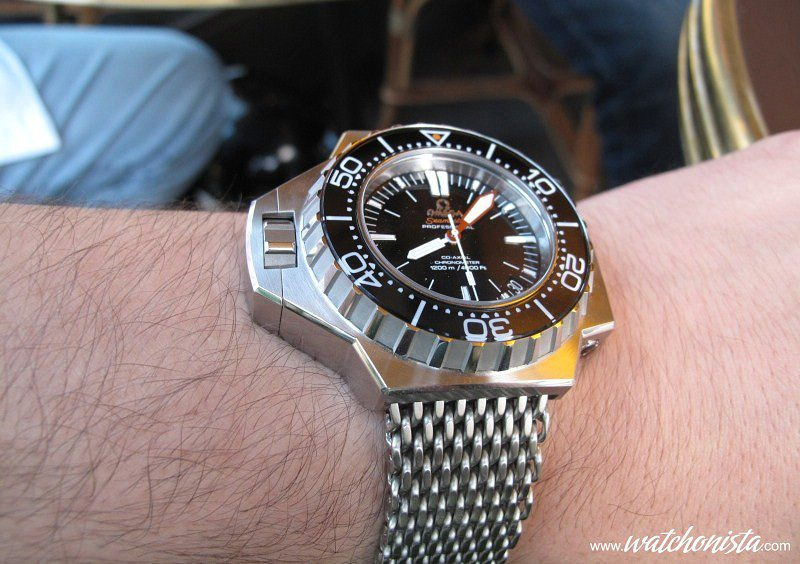
Furthermore, when one talks about watchmaking, the cutting edge technology does not mean the same thing.
In the automotive or the mobile phone fields, the equation is relatively straightforward; the goal is mainly to reach the most advanced technology.
"Mainly" , because if some car makers , leaders from a technological standpoint, are successful, their German counterparts, not always as technically advanced, are even more successful !
In the end, the Teutonic cars take the advantage thanks to their uninterrupted reputation for reliability, prestige and to a certain tradition linked to the German luxury car industry.
From the communists to the capitalists, from the industrials to the organized crime, all, all, all of them did put their renowned bottoms on the Mercedes-Benz stiff leather.
A French rap band (NTM) even sang its ode to the "Benz-Benz-Benz".
Why ? Because Mercedes-Benz is a symbol of tradition. And tradition is a common value to all the cultures.
The reason why I am talking to you about tradition, is because it is the key to the rebirth of the mechanical watchmaking.
In a world where everything moves faster and faster, where one lives in an opulent society steered like a drunken ship, it is reassuring to remember our grand-parents' sacrifices, which allowed for this opulence to exist.
Yet, the mechanical watchmaking's Kryptonite was the quartz.
And there are odd resemblances between the quartz and the silicon: silicon is the main component of the micro-processors that power all our computerized systems, especially the Casio G-Shock.
But also (and specifically?) the fabrication process of a quartz watch is totally standardized, exactly like the production of the sets of silicon escapement devices (compared to the artisanal manufacturing process of a mechanical watch).
Ironically, a well tuned silicon system is amazingly efficient;
the proof is that Technotime, Chopard and Tissot, all of them using silicon hairsprings, won the last International Chronometry Contest.
Yet, the other technology that provides an incredible precision with a silica core is of course the quartz!
The best illustration of this phenomenon is Patek Philippe: the aura of the most prestigious of all brands relies on an uninterrupted tradition of mechanical movements and on the quest for the best quality, by employing the best craftsmen in all Romandie.
So, do we really want a cutting-edge mechanism in a traditional watch?
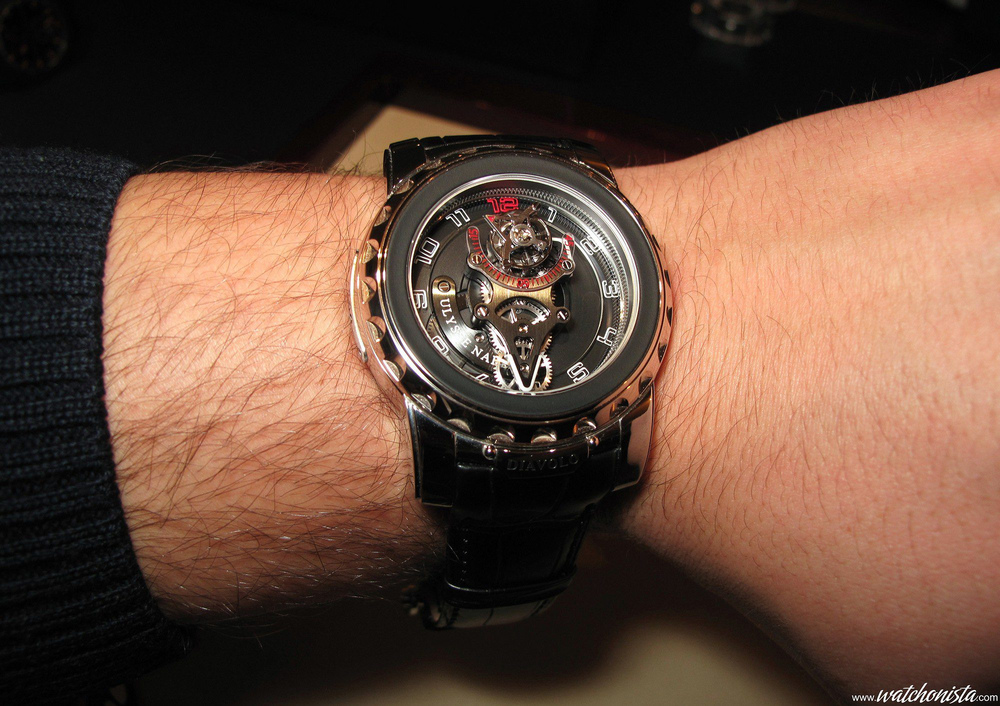
Watchmaking only makes sense if one agrees to stop the technological progress at a given date.
If he had had the adapted tools during the French revolution era, would Abraham-Louis Breguet have integrated silicon into his watches?
In short, the silicon raises the metaphysical question of when does the hard-line mechanical watchmaking stops evolving; does silicon have its place in a traditional watch?
Conclusion:
The butterfly effect is when a minor decision leads to major consequences.
The ironical side of the story is that, after a few generations, the savior of the traditional mechanical watchmaking could become its gravedigger.
The decision to stop the deliveries of Nivarox sets could be an incentive to switch to silicon.
But the latter is double-edged! It could be the greatest revolution in watchmaking since Huygens (well, at least since the Invar), but it also could be the high-tech product that will totally depreciate the Swiss watchmaking tradition...
We are lucky to witness the greatest revolution in watchmaking since the end of the 60's, and the advent of quartz;
like all the revolutions, it could be a top, or a flop. Will silicon join the heaven of the ground-breaking technologies which died too soon? Or will it open the road to new chronometric heights?
Will it crash against the breakers of the reliability's craggy coasts? Will it rescue the Swiss Made from the Dragons' jaws or definitively spoil the already eared Helvetian watchmaking's brand image?
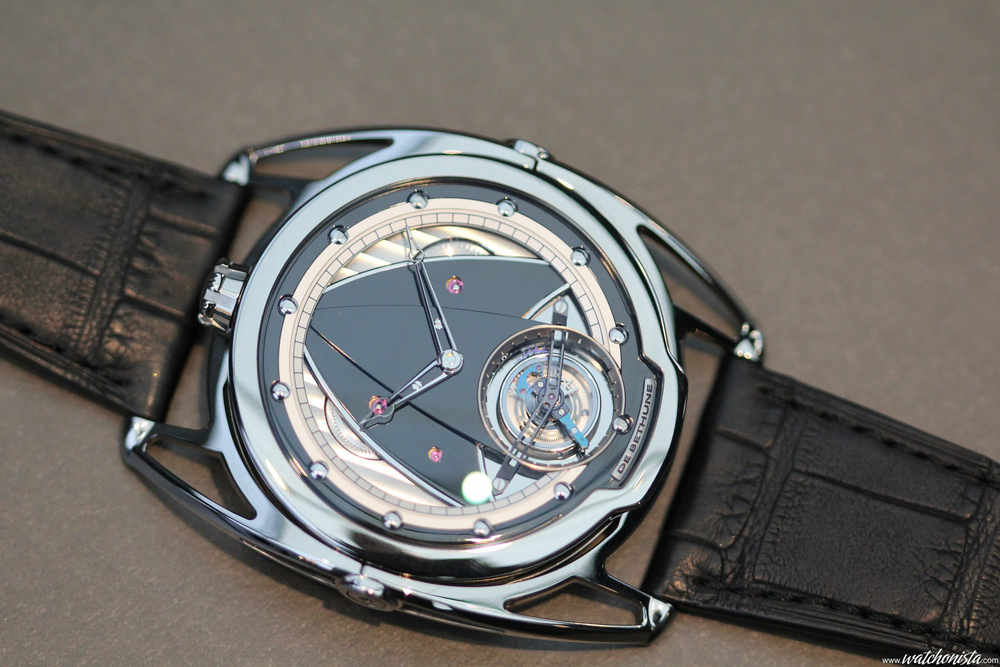